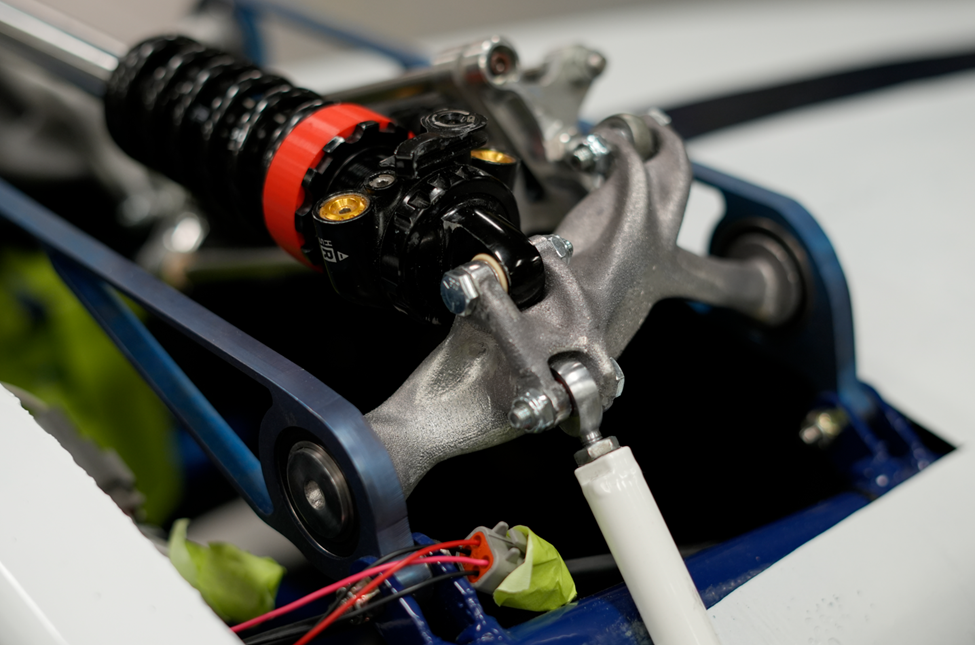
In a showcase of engineering excellence across the university, student organization Nittany Motorsports has partnered with CIMP-3D and 3D Systems to revolutionize their suspension system with the power of additive manufacturing. Competing annually against 100 other student racing teams at Formula SAE Michigan, Nittany Motorsports found that their previous suspension bell crank design cracked after weeks of abuse. A stiffer and more durable solution was needed to transmit wheel motion to the damper.